Computer Controlled Systems Place & retrieve Loads
Automated Storage and Retrieval Systems benefits include labor reduction, increased accuracy and throughput, and a green impact on the environment. Is an AS/RS system right for your distribution center or warehouse?
AS/RS systems are computer-controlled systems that store and retrieve product in distribution centers, warehouses, and manufacturing facilities.
Automated storage has been developing since the 1960s and is the smartest and most sophisticated material-handling system available. Loads are strategically delivered via automation upon demand without the use of manual labor.
Unit-Load AS/RS Systems are larger systems that typically store and retrieve pallet loads. Mini-Load AS/RS Systems move product in cartons, trays, or totes. Both AS/RS have the same configuration: pallet rack with narrow aisles between, allowing a tall masted crane to move down the center of the aisle on a raised metal rail.
When the mast reaches a designated storage location, a carriage travels up or down the mast to the level where the product to be selected is located. A load-handling mechanism is mounted on the carriage and reaches into the location to either place or retrieve the load.
An S/R machine, or SRM, is a crane that includes the mast, carriage, and load-handling device. Most automated storage warehouses use one SRM per aisle; however, more sophisticated systems may have more than one crane per aisle. For lower throughput systems, a single crane may be assigned to multiple aisles and navigate the turn by way of a transfer cart.
There are two types of SRMs – Single-mast and double-mast for extra stability in very tall automated storage systems or warehouses and distribution centers with very heavy loads.
Unit-load automated storage is designed for pallet loads of over 1,000 lbs. or more. Specialized systems can handle heavy loads that are not on pallets, such as furniture or long rolls of materials. A typical unit-load automated storage system can reach up to 100 vertical feet. Most common systems are 40′ or less.
AS/RS systems details are configured with pallet rack single-deep or with multiple pallets stored one behind the other. A telescopic device called the shuttle reaches into the pallet location, slides under the pallet, and pulls it out into the aisle onto the carriage. Older systems use a turret style SRM with a rotating fork. These AS/RS shuttles systems are slower but will interface with any style of pallet rack.
Mini-Load AS/RS is a small-scale system where loads are less than 1,000 lbs. of Unit-Load systems. Usually product is stored in a carton or tote rather than a pallet. There is also a smaller system called macro-load AS/RS which handles loads less than 100 lbs. It virtually operates the same way as a Mini-Load AS/RS.
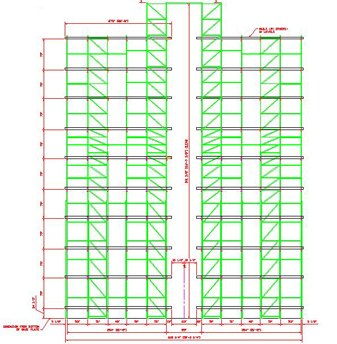
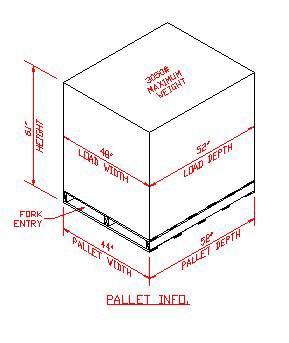
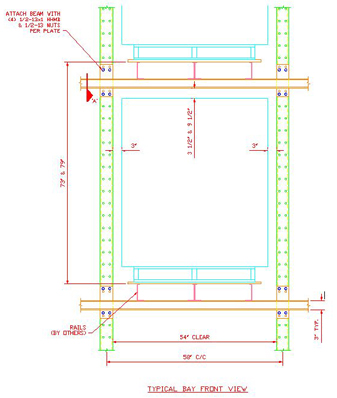
System Highlights:
Automated Storage and Retrieval Systems work by using computer-controlled systems to automatically deposit and retrieve loads from a defined storage area.
Unit-Load AS/RS machines store large loads usually on pallets with a pallet rack structure
Mini-Load AS/RS is typically for lighter loads that are less than 1,000 lbs.
Vertical Lift Modules (VLMs) are columns of trays in the front and back of the module that store and retrieve
Shuttles automatically handle the retrieval and placement of totes, trays and cartons
Horizonal and vertical carousels rotate and store small parts and pieces
Automated Storage and Retrieval Systems support processing and picking in any type of distribution center or e-commerce facility. The accuracy of picking can increase to levels that are close to 99% and the narrow aisles can save up to 85% of floor space that would not be utilized in other storage systems. Let cranes, shuttles, and carousels pick your product and reduce labor costs with an AS/RS system.
For more photos of AS/RS systems, view the UNARCO AS/RS Photo Gallery.
Robots and Computers improve safety
Instead of hundreds of workers in the warehouse, shuttles are used to pick up and retrieve loads. Mini-Load systems use extractors that grasp handles on trays or vacuums that attach with suction. Robotic arms also play a large role in AS/RS Mini-Loads.
Some Mini-Load AS/RS are only 10′ tall while others are 40′. These systems are used to store documents and books as well as parts in warehouses and order fulfillment.
View more photos of AS/RS systems in the UNARCO AS/RS Systems Photo Gallery.