Drive-In vs. Drive-Thru—The Difference
Drive-In Rack and Drive-Thru racking are terms that are often used interchangeably. In some environments, it can be difficult to differentiate between the two. Typically, Drive-In racking requires operators to drive into the racking system from one side and remove pallets from the same entry point. Some Drive-In Rack systems have a wall or are otherwise closed at the opposite end.
A simple way to identify a Drive-In Rack Systems is its LIFO inventory management. Product is rotated in a Last-In, First-Out inventory manner because of the single entry/exit point.
The draw to a Drive-In Rack system is its extremely efficient storage concentration. Pallets are stored back-to-back without aisles for exceptionally dense storage. This style system is an excellent solution for product that is not time- or date-sensitive, or for fast moving pallets that are rotated frequently.
UNARCO offers many variations of Drive-In/Drive-Thru racking with structural or roll formed product. The Spacesaver, tapered arm allows pallets to slide easily into the bay. It has a tapered edge at the front entry point.
Drive-In Rack is perfect for products that need cold or freezer storage, especially for applications that have a large number of similar product loads. Since freezer warehouse space is so expensive to operate, it is important to maintain a dense storage area.
Drive-In Rack also helps protect fragile product loads that cannot be stacked while keeping product spacing as dense as possible. However, inventory rotation is limited to LIFO for Drive-In systems even for double entry drive-in projects.
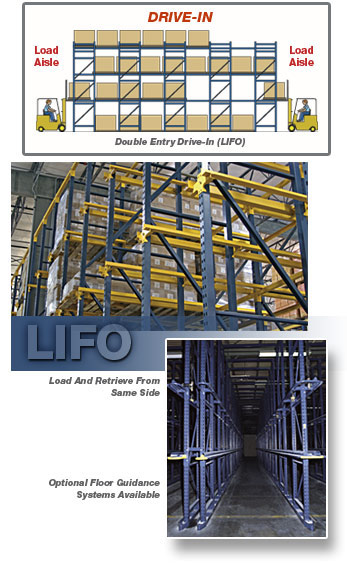
System Highlights:
Drive-In Racking systems are cost-effective, high-density storage.
Lift trucks enter the rack to place and access pallets
Loads are supported on rails attached to pallet rack uprights
Tight storage of pallets or boxes
Drive-In Rack works well against a wall to increase rack depth and use maximum vertical space
Last-In-First-Out (LIFO) method for product picking
To create tight storage of pallets and boxes and eliminate aisles, Drive-In Rack is a very cost-effective application. This system uses no mechanized or gravity means to flow product, but is the densest static storage application available, often for the most reasonable price.
For more photos of Drive-In systems, view the UNARCO Drive-In Photo Gallery.
Drive-In Cube Utilization Requires Forklift Safety
Drive-In Rack operators must be very careful not to damage the pallet racking. Since pallets are stored so densely and a driver must enter the pallet racking system with only a small clearance on either side, a Drive-In Rack system must be checked for damage frequently. As soon as pallet rack damage is noticed, it must be reported and properly repaired or replaced. A strict safety doctrine must be adhered to with a Drive-In Rack system.
For more photos of Drive-In Rack view the UNARCO Drive-In Rack Photo Gallery.